11-01-2021
Our manufacturing process explained: mechanical machining
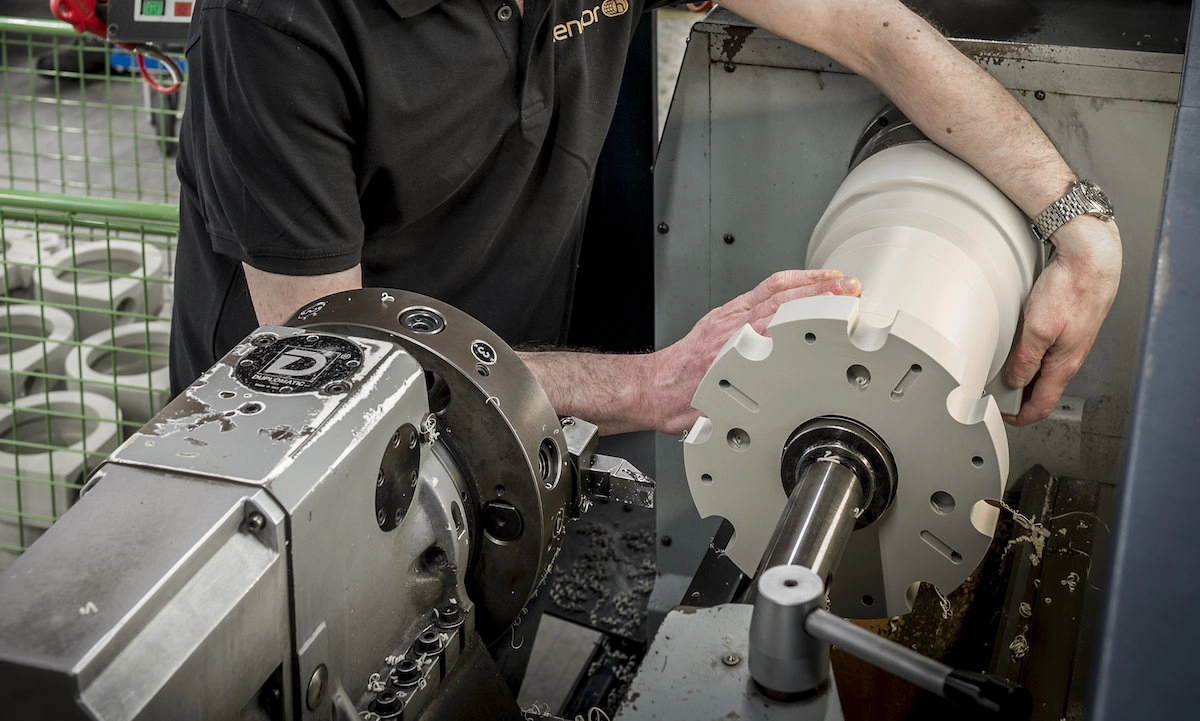
We believe that designing and manufacturing our products goes hand in hand with a great deal of expertise and craftsmanship. In this series of five blogs, our goal is to elaborate on our manufacturing process. How do our pumps & filters arise from polypropylene (PP) to an end product? Step 2: mechanical machining.
Precision is key when it comes to manufacturing pumps & filtration systems. To make sure that all the injection molded parts connect seamlessly, we mechanically machine them. In our manufacturing process, this step entails milling, or turning. The result: smaller tolerances, and a better end product. In our opinion, this is an extra step which sets our products apart from others. It’s all about the details, and we make sure every detail is correct.
Precision is key when it comes to manufacturing pumps & filtration systems. To make sure that all the injection molded parts connect seamlessly, we mechanically machine them. In our manufacturing process, this step entails milling, or turning. The result: smaller tolerances, and a better end product. In our opinion, this is an extra step which sets our products apart from others. It’s all about the details, and we make sure every detail is correct.
Differences between milling and turning
The process of milling and turning is quite similar. In both situations, a cutting tool shears off layers of the workpiece in order to create a desirable shape. At Hendor, we have specialists who perform these processes with utter precision.
The difference between the milling and turning method is the object that rotates. During the milling process, a particular component is fixed while a rotating milling cutter moves around it. With turning, the cutting tool stays at one place and the workpiece rotates on a lathe. Turning is mostly used with round objects that require symmetry along their central axis – which is the case with most of our components. In addition, the turning process takes less time than the milling process.
The difference between the milling and turning method is the object that rotates. During the milling process, a particular component is fixed while a rotating milling cutter moves around it. With turning, the cutting tool stays at one place and the workpiece rotates on a lathe. Turning is mostly used with round objects that require symmetry along their central axis – which is the case with most of our components. In addition, the turning process takes less time than the milling process.
Least material waste possible
Logically, this step creates leftover material. We find it very important that we reduce our product waste as much as possible. Therefore, we collect all the sheared off chips, and send them to a company which reforms them again into granulate – this goes for our PP- as well as PVDF chips.
In the next blog, we will elaborate on the third step to manufacture a Hendor end-product. Make sure to follow us on LinkedIn, where we will announce the publication.
In the next blog, we will elaborate on the third step to manufacture a Hendor end-product. Make sure to follow us on LinkedIn, where we will announce the publication.