06-01-2021
From polypropylene to Hendor end product
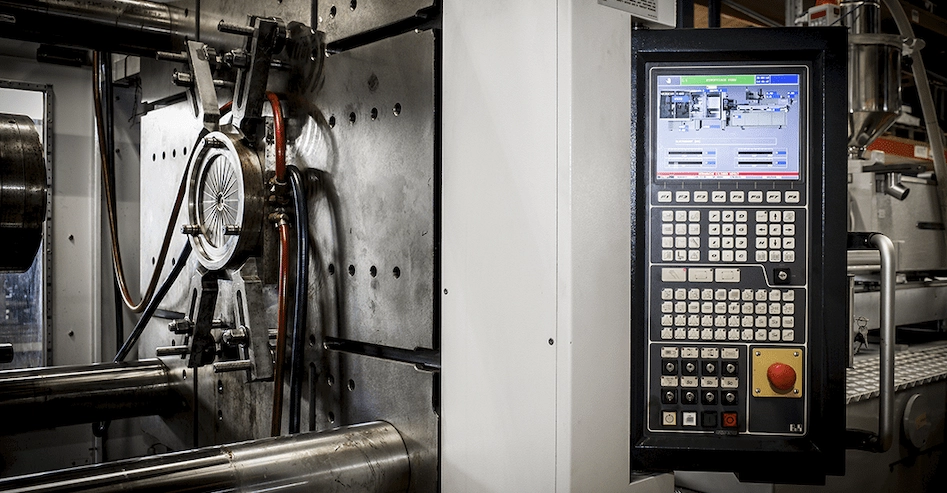
We believe that designing and manufacturing our products goes hand in hand with a great deal of expertise and craftsmanship. In this series of five blogs, our goal is to elaborate on the Hendor manufacturing process. How do our pumps & filters arise from polypropylene (PP) to an end product? Step 1: injection molding.
What is injection molding?
Many of the PP and PVDF components which we use for our products are injection molded, all at our Hendor headquarters. In short, injection molding is the process of melting down granulate at high temperature and pressing it in into a mold. After cooling down, you end up with a specific pump- or filter part. Before we start the actual injection molding process, there are some crucial factors to take into account: - Temperature - Recrystallization - Raw materials - Additives
Key determinants for injection molding
Logically, every product can be used for different applications. Depending on our client’s use of the product, i.e. the specific chemical solutions that will be pumped or filtered, we need to specify the mix of raw materials and additives. This mix determines the temperature at which it will be melted, as well as the cooling time. For the cooling time, it is incredibly important that this phase takes the right time. Waiting too short can cause the inside of the material to still be warm, and therefore transform the shape. In addition, internal tension can occur which decreases the chemical resistance of the product.
We have specifications for every product that is fully manufactured by ourselves. Our team of experts makes sure that these guidelines meet the high-quality demands. These requirements consist of the mixture of base materials and additives, temperature specifications, and cooling time.
Mostly, we work with PP, because it’s a strong material with high chemical resistance, suitable for high temperature applications. We only use high quality PP granulate which is produced in Europe. Before it is melted, we check the analysis certificate of our PP granulate to make sure it qualifies for our products.
We have specifications for every product that is fully manufactured by ourselves. Our team of experts makes sure that these guidelines meet the high-quality demands. These requirements consist of the mixture of base materials and additives, temperature specifications, and cooling time.
Mostly, we work with PP, because it’s a strong material with high chemical resistance, suitable for high temperature applications. We only use high quality PP granulate which is produced in Europe. Before it is melted, we check the analysis certificate of our PP granulate to make sure it qualifies for our products.
The actual injection molding process
The right mixture of granulate and additives is put into the machine. Every time, a calculated amount of this mixture is transported to a ‘melting chamber’. There, it melts at a temperature between 220 and 240°C. Thereafter, the melted material is pushed into the mold with high pressure. In this mold, a cooling fuel is added to increase the cooling time. Then, the mold opens, and the component can be taken out. It is put to rest for further cooling. The total process time of injection molding a pump- or filter part takes approximately five minutes. At Hendor, we don’t immediately use our injection molded parts. Depending on the type and thickness of material, the rest time takes from two weeks up to two months. This way we make sure the part is completely set. Furthermore, we temper our products to get rid of possible internal tension within the part. Lastly, we finish the product to secure the required measurements. This is essential for the rest of the production process.
In the next blog, we elaborate on the second step to manufacture a Hendor end product. Make sure to follow us on LinkedIn, where we will announce the publication.
In the next blog, we elaborate on the second step to manufacture a Hendor end product. Make sure to follow us on LinkedIn, where we will announce the publication.